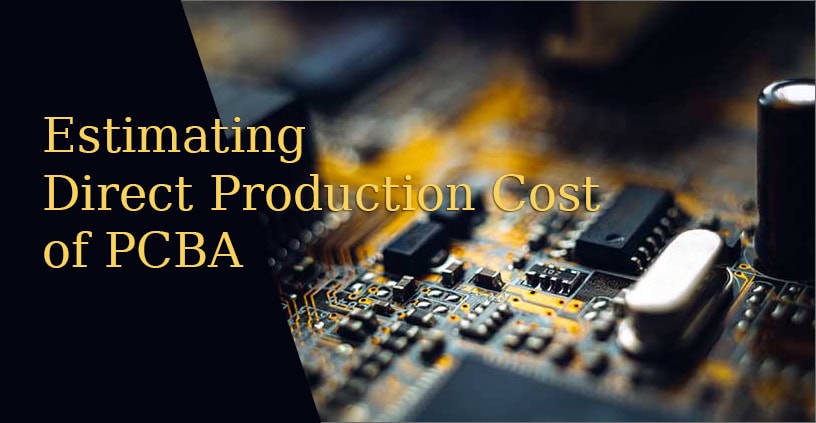
Estimating Direct Production Cost of PCB Assembly Job
Estimating the direct production cost of the PCB Assembly job in Sparrow ERP is accomplished by setting up some key parameters and attributes one time. Currently, The Sparrow ERP considers the following items in calculating direction cost calculations.
- Component costs (based on Bill of Material).
- Assembly Cost (based on cost added in Sales order).
- Labor cost (based on parameters set in the workcenter).
- Equipment cost (based on parameters set in the workcenter).
Direct costs are again of two types in the system; Pre-production cost and Post-production cost. Pre-production cost is derived from the estimation of the usage of material and resources. Post-production cost is calculated based on the actual usage of components and resources.
Component Costs:
The sourcing activity needs to be finished before production starts and as a result we have total cost of components. The Sparrow ERP’s Purchase plan module allows users to automatically fetch prices and stock availability of components from Bill of Material.
Assembly Cost:
Cost of assembly is either entered manually by operator or using Sparrow ERP’s in-built assembly cost calculator.
Labor Cost:
You can define the hourly rate of operation in Sparrow ERP’s workcenter. Workcenter is a virtual/physical place where actual work is done. To carry out the work resources are added to the workcenter. Each work center resource can carry cost attributes. For example, in the Manual Soldering workcenter main resource is the operator; an hourly cost of an operator can be set in this case.
Equipment cost:
Same as Labor cost, equipment to carry out work is added in Workcenter. Each equipment carries the cost of usage. The cost of usage per hour can be added per equipment.
All these parameters when set correctly, can result in a pretty accurate calculation of direct cost of the PCB Assembly. When production job starts, the system knows which workcenter is being used. The system also allows flexibility to choose a particular resource at the start of the operation. At the end of all operations, we have a complete picture of how many resources are used for how long and that gives us the capability to calculate direct production cost.